Adaptive Strategies: What is the New Normal?
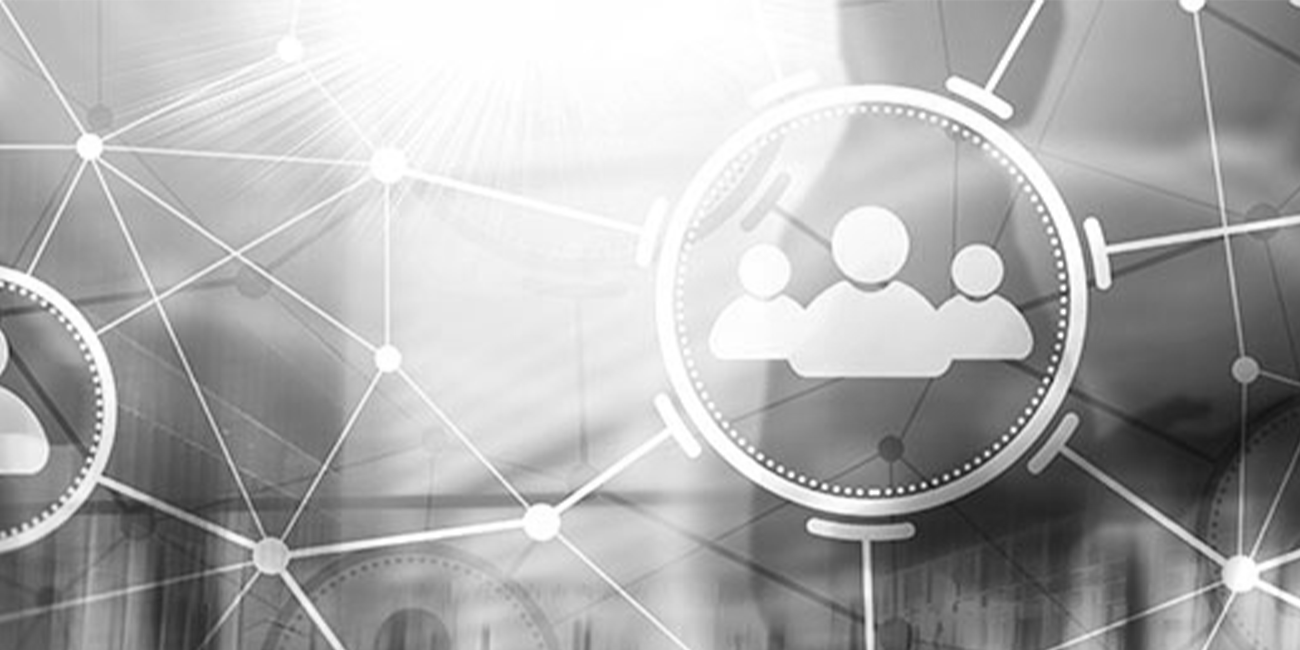
Adaptive Strategies: What is the New Normal? (April 20, 2020)
Looking across the country, the real estate and construction industry is being impacted in a multitude of ways in different regions. While urban centers like New York and the Bay Area have experienced across the board work stoppages due to government orders, much of the rest of the country is managing to respond to CDC and state guidelines with adaptive strategies, though job site efficiency can range anywhere between 30% to 70%.
At PMA, we’re coalescing the strategies we are seeing, sharing them in an effort to offer insight to project challenges you may be facing now or in the future.
Have some adaptive strategies you’d like to share? We’re all ears.
We’re all #inthistogether.
How are project teams minimizing losses in efficiency and production in the current environment?
With pre-work winding down, a large tenant buildout in Chicago was scheduled to move full steam ahead on April 1. Early news of the pandemic’s spread prompted the General Contractor (GC) on the job to implement selected restrictions to enhance project safety that also translated into an immediate loss i [officeArt object] n productivity. State mandates soon followed and, due to distancing requirements, the allowable workforce on the 4-floor project was slashed from 140 people per day to 60, further impacting efficiency.
This early stage of the project was largely defined by framing and MEP/FP rough-in efforts. The project team considered the specific cost and schedule impacts of a number of strategies and opted to stagger MEP/FP trades during typical working hours while moving framing to second shift. The approach of staggering start times is expected to result in nearly twice the production efficiency of having all trades overlapping during two shifts, thus minimizing impacts to schedule.,
Does the project GC have procedures in place to continually monitor and manage procurement in this fluid environment?
On a west coast project, it was identified that custom wood doors sourced from Oregon could not be manufactured and delivered to the project site when they were needed, so equivalent metal doors from a local vendor were substituted, allowing the team to maintain contractual delivery dates.
Can Architects and Engineers effectively perform essential Construction Administration (CA) services remotely?
Most local A/E teams face limitations on if and/or when their staff may visit project sites. While some firms have been able to utilize photo and video technology to meet CA contractual obligations, others are adapting to scheduled site visit appointments organized by the GC to ensure that all key personnel are available to accomplish a productive walk through.
Out of town A/E personnel facing travel restrictions are considering engaging local architects to conduct CA services on their behalf.
Will lenders approve payment for offsite stored materials absent an onsite inspection?
Even as projects slow dramatically, teams must still meet strict contractual obligations involving the GC and its subcontractors relative to offsite stored materials. Those representing lenders, when unable to observe and inventory offsite stored materials for payment validation purposes, are similarly challenged when they are asked to recommend payment without a physical presence. On a job in the Bay Area where onsite work is stalled due to local restrictions, all parties worked collaboratively to establish acceptable standards of photo and video documentation in order to meet obligations and maintain cash flow.
How can demobilized projects position for success as we look forward to eased restrictions?
Some states are beginning to discuss the development of guidelines for easing mandated restrictions in the coming weeks. In an effort to stay ahead of the curve, a project team in California’s Bay Area whose site has been on hold for weeks is actively engaged in strategic conversations with subcontractors about their capacity and priorities in providing needed workforce levels once the job recommences.
Remobilization plans are also beginning to be formulated and potential cost impacts studied based on anticipated production of “skeleton” staffing to address critical tasks.
People Power: Four Ways to Improve Multifamily Project Predictability
Tight timelines. Strict budgets. Complex systems. On the surface, multifamily projects are about coordination, cost control, and construction logistics. But beneath it all, the most consistent driver of project success...